Westie
Active Member
- Oct 16, 2008
- 1,109
- Boat Info
- 2001 260 Sundancer towed with the power of an IFORCE V8
- Engines
- 7.4 L Bravo III
For the past while I would always have some water in the bilge and didn't know where it was coming from. It was never a lot but last time I was out it seemed to be more than usual. So on Wednesday I climbed into the bilge while my wife backed the truck down the ramp. As soon as the transom was in the water I noticed some water in the bilge.
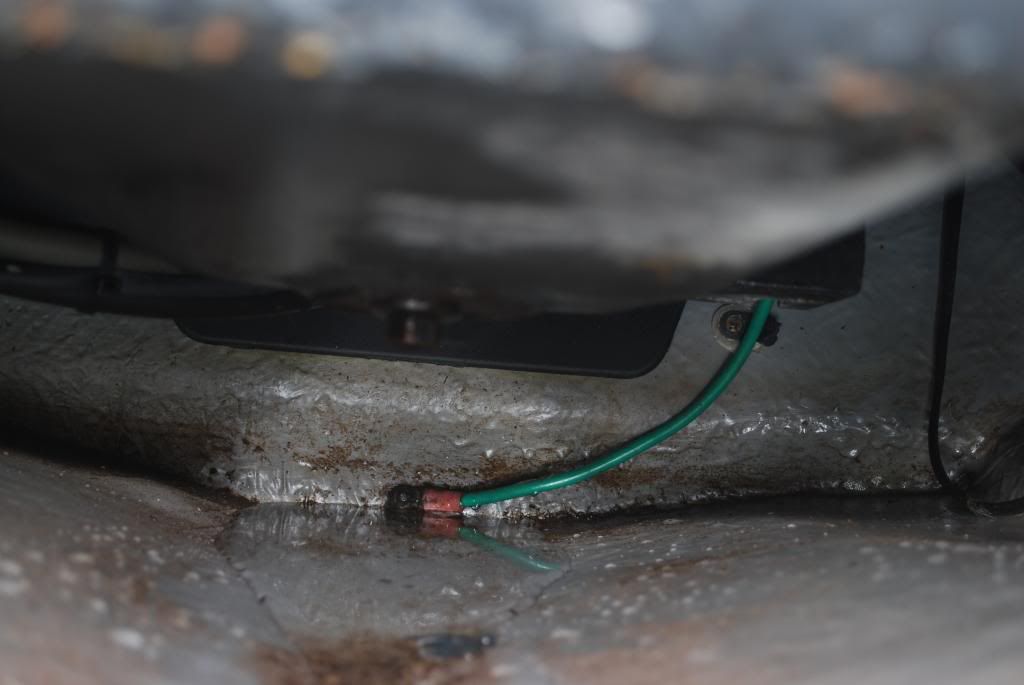
It had to be the transom drain plug so when I got home I took it off. I have to say I was not impressed with the workmanship. The hole was drilled too big. It was 1.189" in diameter, for a 1" OD fitting. As a result two of the screws were right on the edge of the hole and where pretty much torn out. The sealer around the fitting was just cheap crap, wasn't even stuck to the flange. Number 6 screws were all that were used.
So today I am laying in a couple of layers of glass mat to build up the hole so that I can reinstall the flange. Of course to get to the back of it to attach the bonding wire I have to remove the batteries and the blower so I can get access to the very bottom of the transom from the inside..
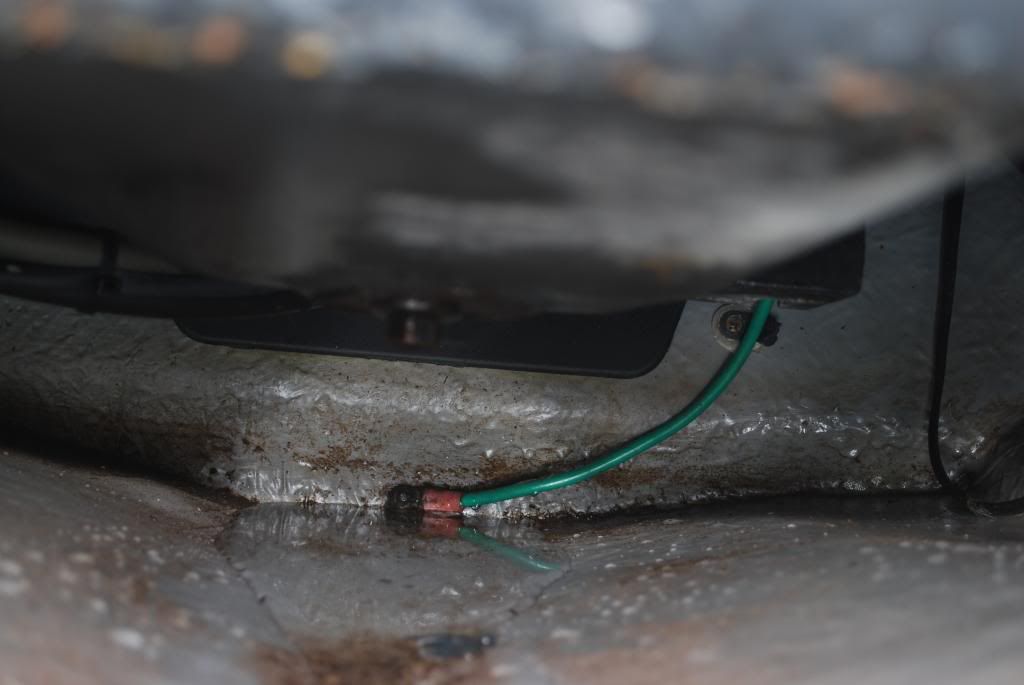
It had to be the transom drain plug so when I got home I took it off. I have to say I was not impressed with the workmanship. The hole was drilled too big. It was 1.189" in diameter, for a 1" OD fitting. As a result two of the screws were right on the edge of the hole and where pretty much torn out. The sealer around the fitting was just cheap crap, wasn't even stuck to the flange. Number 6 screws were all that were used.
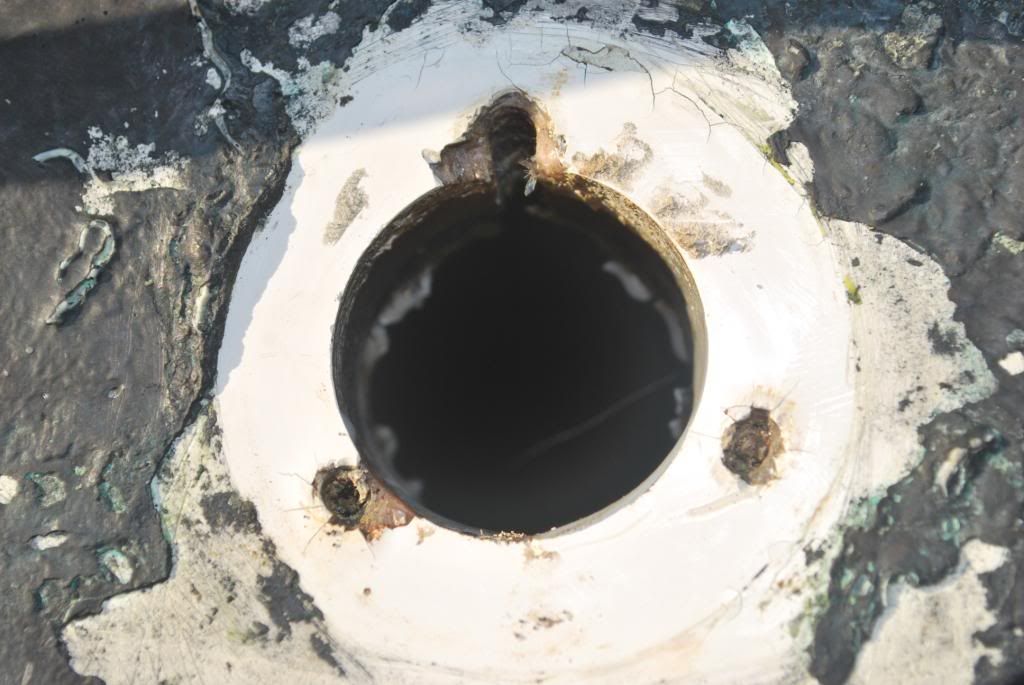
So today I am laying in a couple of layers of glass mat to build up the hole so that I can reinstall the flange. Of course to get to the back of it to attach the bonding wire I have to remove the batteries and the blower so I can get access to the very bottom of the transom from the inside..