WTP07
New Member
- Jul 16, 2008
- 219
- Boat Info
- 1985 Cruisers Inc
Ultra Vee 336
- Engines
- T454 Crusaders - 700HP
Same piece of wood, cut, shaped, sanded, and 2 coats of epiphanes so far...only another 13 coats or so to go...
Stay tuned...
R.
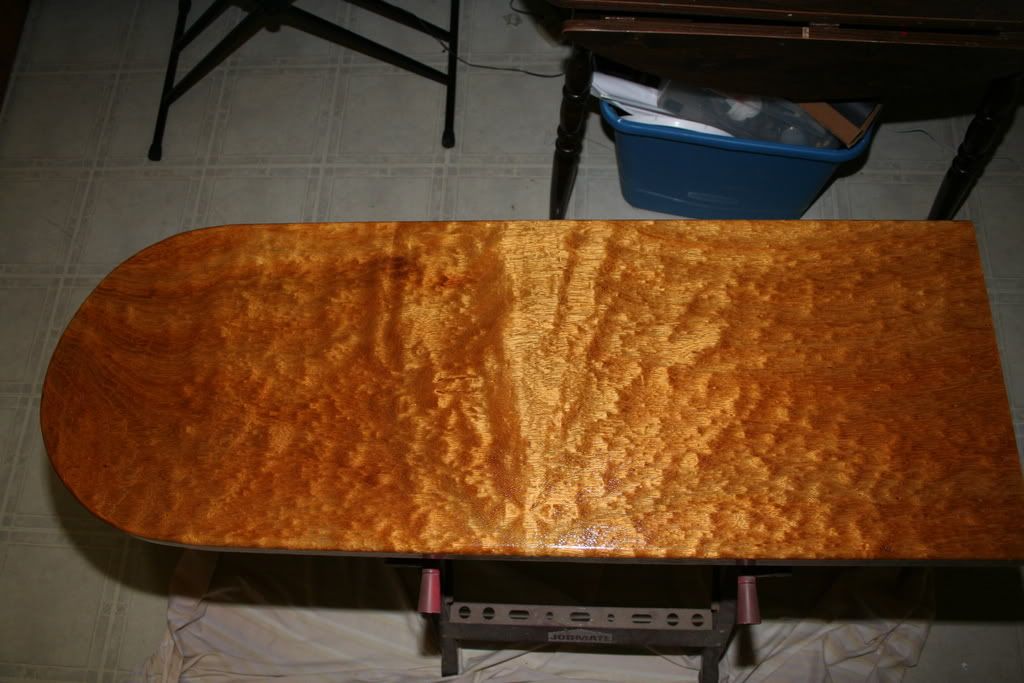
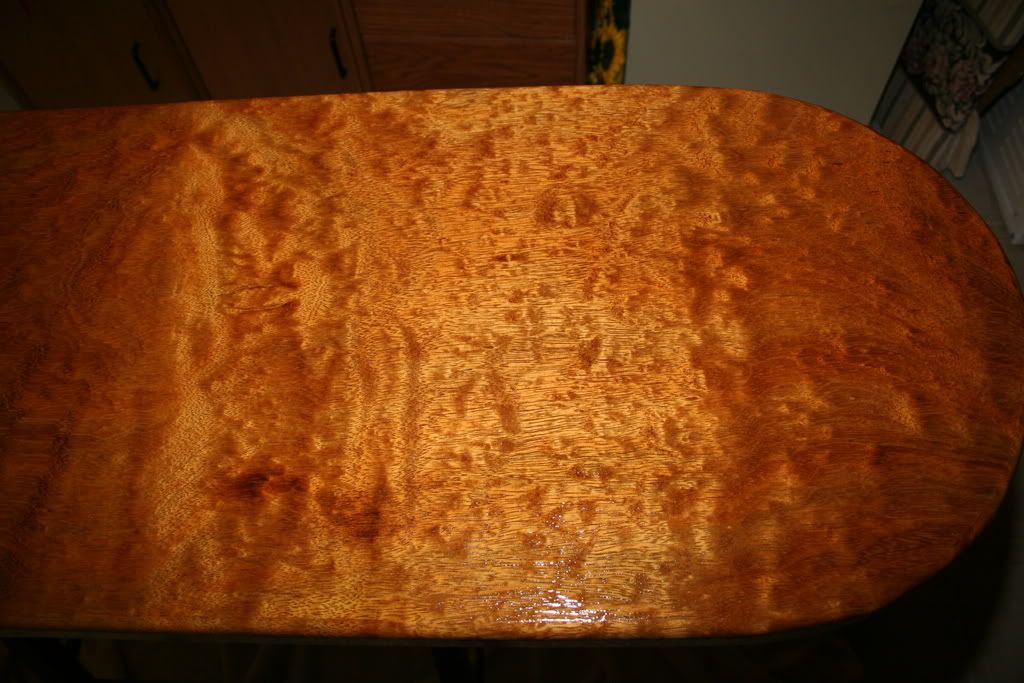
Stay tuned...
R.
Last edited: